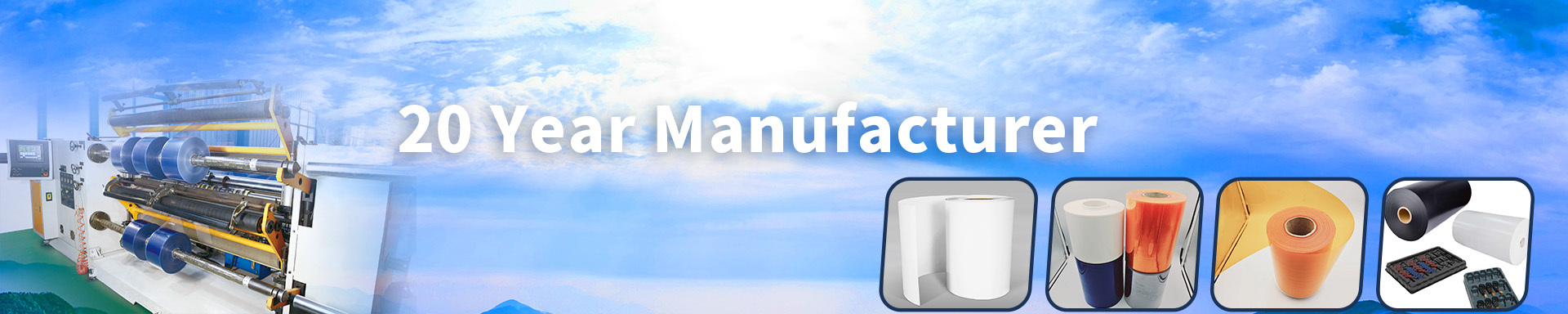
- Home
- >
News
Antistatic and Thermoformable PET Film: Wonders of Versatility by In the bustling metropolis, one young, innovative entrepreneur named Lily Chang was going to change the world of materials. It was the year 2024, and Lily had just discovered the astonishing properties of antistatic and thermoformable PET film. Little did she know that this would be an exciting journey that would affect many industries and change lives. The finding of sustainable and practical solutions for day-to-day problems had always remained close to her heart. Progressing further in the world of materials, she found anti-static thermoformable PET film. Curious about its capabilities, she started to find ways where it can be used. It was on one such day while sitting in the small office and gazing out at the skyline of the city that she finally thought that with such film, she might print out A4 sheets that are singularly special. She was so thrilled by the very idea that soon she got down to work on it. Lily then called a local printing company and described her idea. To begin with, the printing company was somewhat skeptical, but once they had samples of the PET film, skepticism turned into interest. Together they began experimenting with different ways of printing the film and soon discovered that it could bear excellent bright prints. The news began to circulate about Lily's printable A4 PET film sheets. Their unique features increased the attraction of students and professionals alike towards these sheets. Because of the antistatic property, prints do not possess static electricity and hence are easily handleable and storable. The thermoformable nature of the film opens more ways of creative usage, such as making note cards or bookmarks in an arbitrary form. As the news spread, Lily was invited to present the product at a local trade show. She was happy to expose her innovation to more people, so she accepted the invitation. The booth was flooded with visitors during the trade show. Still, people were further surprised to see the versatility of PET film. One of them was Alex, a graphic designer who was pretty impressed and visualized using these sheets for his design projects. Alex walked up to Lily and started a conversation with her. Soon, both found that they shared an interest in innovation and design. Alex also mentioned to her about the PET film for customized packaging and how she could join on a project to work with it. The idea thrilled Lily, and they did not delay in starting their work. They started researching all types of packaging needs and came up with a few ideas. One of the ideas was to do some innovative packaging for a local cosmetics brand. The cosmetic company was looking for varnish and striking green packaging solutions. Lily and Alex presented their idea of using antistatic and thermoformable PET film. Interested, the company decided to give it a try. Thus, Lily and Alex were putting great effort into designing packaging and then actually making it. They used the thermoformable property of the film to create custom shapes that would fit the cosmetics products perfectly. The antistatic feature would protect them against electrostatic discharges during transport and storage. The result was amazing. The packaging was beautiful, but not only that-it was functional. It called the attention of the consumers and soon became a hit. The cosmetics company loved the result and ordered more of such packaging. Buoyed by the success, Lily and Alex continued to explore other applications of the PET film. They soon turned their attention to food and pharmaceutical industries. Safety and freshness are key factors in the food industry. Lily and Alex realized that the antistatic and thermoformable PET film would assist in maintaining the freshness of the food and containing no contaminants. They had a package designed with the local food manufacturer for his products. This proved ideal for properties such as packaging of food. Antistatic dispensers prohibited the adherence of dust and other particles onto the packagings, while the thermoformable property allowed customized shapes, which fit different food items. In this case, this turned out to be effective yet attractive packaging. The pharmaceutical industry demands sterile and safe packaging. Lily and Alex worked with a pharmaceutical company to develop packaging that would meet these demands. The PET film instantiated an antistatic property of the film which prevented the build-up of the charges capable of damaging some sensitive medications. The thermoformability was adjustable for those custom-designed packaging meant to secure the drugs during transportation and storage. Here, both Lily and Alex had a reason to look forward to further opportunities once their projects were successful in food and pharmaceuticals producing industries. As a matter of fact, they were invited as guest speakers in industry conferences where they shared their experiences with others. As they got more and more popular, one day, Lily and Alex were approached by a local interior designer. The interior designer wanted something very special for his next big decoration project. Lily and Alex recommended the PET film. They worked with designers for the creation of custom walls and decorative panels. The thermoformability of the film allowed for creative designs and figures, along with an antistatic feature of the decorations, which made them without static electric properties, thus giving an amazing look of space. In the field of glass decoration, Lily and Alex also carved their niche. They also developed a method of applying the PET film to glass surfaces to make privacy screens, decorative windows, and other unique glass features. Because of the properties of this film, installation and removal were pretty easy; thus, it found its place in residential and commercial usages. As the year drew to a close, Lily and Alex looked back with pride to see how it had been. They had taken an easily available material and molded it into a multiutility solution making a difference in various industries. From printable A4 sheets to creative packaging, decoration items, up to glass enhancement, the list of applications for thermoformable PET film is endless. Their story of Lily and Alex had emphasized the force of innovation and teamwork. They had proved that with just a little creativity and determination, even one simple material could go a long way into changing the world. They knew that their journey of thermoformable and antistatic PET film was far from over as they looked to the future. Actually, they were pretty excited about the new applications of the material and the new opportunities. Conclusion: This is quite a remarkable story involving discovery and use of antistatic and thermoformable PET film by Lily Chang and Alex. It's reached into printing and packaging, food, pharmaceuticals, decoration, and the decoration of glass. Their traits have proven-you just need to think differently, and you will definitely find something which is suitable and applicable in everyday industrial problems. With ever-growing sustainability concerns and the need for versatile materials, antistatic, and thermoformable PET film possibly holds a bright future for any who would dare to work and venture into it.
Anti-Static, Thermoformable PVC Film—Emerging Use One fine morning of [date] in the hustling city of [city name], a young entrepreneur, Lily Zhang, demonstrated the amazing versatility of the anti-static, thermoformable PVC film. Since she was a child, Lily was always interested in finding creative solutions for packaging and decoration problems. The first interest in PVC film came when she realized the growing needs for materials that combine functionality and aesthetics. Only the good and careful investigation of this topic, along with the examination, have greatly nurtured this interest, leading to the exploration of the peculiar features of anti-static thermoformable PVC film. At the beginning of this story, Lily visited a local packaging factory. Sensitive electronic parts, being packaged at this factory, would be destroyed by the static electricity. Their acquaintance was made with anti-static PVC film. The ability of the film to dissipate static charge caught immediate attention with the managers of this factory, which decided to give it a try. The PVC film was put on at the packaging stage, and Lily did it with the help of the factory team. The result was that the problem of static electricity disappeared, and the products packed could not be damaged in any way. Improved packaging gave a nicer look to the products, which was more catching for the customers. Not content with this single success, Lily applied her mind to the food packaging industry. She knew the importance of safety and presentation of food. With an anti-static PVC film, she was in a position to offer a solution that would protect the food from static charge, besides offering a clear and hygienic method of packaging. She toured some food processing factories and could demonstrate to them the feasibility of the PVC film. The plant managers could not believe how durable the product was, and how clean it was to use. They bought into the product and were now using the film to package fresh fruits, fresh vegetables, and even processed snack foods. The food can now be transported and stored without going bad and contaminated by any foreign matter. Next was pharmaceutical packaging. The requirements were much tougher: sterile packaging that protected the drugs from moisture and static electricity, yet conformed very strictly with the rules. Lily's anti-static PVC film proved up to the task. She worked in cooperation with pharmaceutical companies for the development of special packaging solutions. Examples of packaging made from this film are pills, tablets, and liquid preparations. Because this material is thermoformable, the form and size of packaging are easily managed to precisely fit a product. Anti-static properties protect medication from static damage, while clarity of the film allows for the possibility of seeing through for quality control. In interior decoration, Lily has found a completely new domain of application for the PVC film. She conceived using it in making those really unique and eye-catching designs in the apartment. She went and started co-operating at first with interior designers, then architects. Together, they were creating such a thing as wall coverings, so-that ceiling paneling, some decorations. Consequently, the PVC film could be let loose with abandon. It could be embossed printed, several patterns and colors could be offered or mixed, thus providing the designer with an ample latitude in working on interiors that are very personalized and chic. It was also easy to install and maintain and for these reasons preferred, not only by households but business establishments as well. Yet, in the field of glass decoration, Lily's PVC film shone once again. She has also created the special adhesive-backed PVC film, which can be directly applied to the surface of glasses to add not only a decorative touch but also privacy and UV protection. The journey of Lily with the anti-static, thermoformable PVC film was not that smooth. She was rejected by convinced clients who would not easily convert to another material. But through her persistence and hard work, she was able to overcome these obstacles and prove the value of the PVC film. With the success of Lily getting announced everywhere, anti-static thermoformable PVC film began to contact more and more industries. For example, automotive interior and aerospace components, the application of it was burgeoning. Actually, Lily's innovation had really made a miracle in many fields. Today, Lily is regarded as one of the authorities in packaging as well as decoration material. And her case is used to inspire others who, in drastic means, seek solutions to their everyday troubles. Because of Lily's vision and insistence, antistatic thermoformable PVC film is now indispensable in many industries. This thermoformable film has found application within the fields of packaging, food packaging, pharmaceutical packaging, decoration, and glass decoration because of its anti-static property. Unique qualities and infinite creativity opened up new paths of innovation and invention. Behind this successful innovation stands Lily Zhang, a young entrepreneur who dared to dream and make a difference.
"The Versatile World of Colored PVC Film: Transforming Industries and Spaces" In today's fast-paced and ever-evolving world, innovative materials are constantly emerging to meet the diverse needs of various industries. One such material that has been making waves is colored PVC film. With its wide range of applications and remarkable properties, it has become a game-changer in the fields of packaging, pharmaceutical packaging, food packaging, decoration, and glass decoration. Time: Over the past few years. Location: Worldwide. Characters: Manufacturers, designers, consumers, and industry experts. I. Introduction Colored PVC film, with its vibrant hues and durability, has captured the attention of businesses and individuals alike. This versatile material offers a plethora of benefits, from enhancing product visibility to adding a touch of elegance to interiors. Let's explore how it has been making an impact in different sectors. II. Packaging Industry In the packaging industry, the quest for materials that are both functional and visually appealing is ongoing. Colored PVC film emerged as a promising solution due to its ability to protect products while also attracting consumers' attention. Manufacturers began incorporating colored PVC film into their packaging designs. For consumer goods packaging, the film was used to create eye-catching boxes, pouches, and wraps. In the food packaging sector, it was utilized to package snacks, candies, and other perishable items. The film's moisture-resistant and durable properties ensured that the food remained fresh and protected. In pharmaceutical packaging, colored PVC film was employed to distinguish different types of medications and provide a tamper-evident seal. The clear and colorful film allowed for easy identification of the product, while also ensuring its safety. The use of colored PVC film in packaging had several positive outcomes. Firstly, it increased product visibility on store shelves, leading to higher sales. Consumers were drawn to the attractive packaging, which made the products stand out from the competition. Secondly, the film's durability provided excellent protection to the packaged items, reducing the risk of damage during transportation and storage. Additionally, in pharmaceutical packaging, the tamper-evident feature gave consumers confidence in the safety and authenticity of the medications. III. Decoration As people's aesthetic preferences continue to evolve, there is a growing demand for unique and creative decoration solutions. Colored PVC film offered a new way to add color and texture to interiors and exteriors. Interior designers and architects started using colored PVC film to transform spaces. In homes, it was used to create feature walls, backsplashes, and furniture accents. The film's easy application and removal made it a popular choice for those looking to update their living spaces without a major renovation. In commercial spaces such as offices, restaurants, and retail stores, colored PVC film was used to create branded environments and enhance the overall atmosphere. The film could be printed with logos, patterns, and designs, adding a personalized touch to the space. The use of colored PVC film in decoration had a significant impact. It allowed for quick and cost-effective transformations, enabling businesses and homeowners to achieve their desired look. The film's variety of colors and finishes provided endless design possibilities, allowing for unique and personalized creations. Moreover, its durability ensured that the decorations would last for a long time, even in high-traffic areas. IV. Glass Decoration Glass is a popular material for both functional and decorative purposes. However, it can sometimes lack privacy or require an added touch of elegance. Colored PVC film offered a solution to these challenges. Colored PVC film was applied to glass windows, doors, and partitions to add privacy, reduce glare, and enhance the aesthetic appeal. The film could be frosted, tinted, or printed with designs, providing a variety of options to meet different needs. In residential settings, colored PVC film was used to create privacy in bathrooms, bedrooms, and home offices. In commercial spaces, it was used to divide office areas, create conference room partitions, and add branding to storefronts. The application of colored PVC film to glass had several benefits. It provided privacy without sacrificing natural light, creating a comfortable and inviting environment. The film also reduced glare, making it easier to view screens and work in bright areas. Additionally, the decorative options offered by the film added a touch of style and sophistication to the space. V. Conclusion Colored PVC film has truly revolutionized various industries with its versatility and functionality. From packaging to decoration and glass decoration, it has proven to be a valuable material that meets the diverse needs of today's consumers and businesses. As technology continues to advance, we can expect to see even more innovative applications of colored PVC film in the future. Whether it's enhancing product visibility, creating unique interiors, or adding privacy to glass, this remarkable material is sure to continue making an impact.
PVC Film for Blister Packaging: A New Manufacturing Facility to Be Launched in 2023 August 20, 2023 — Houston, Texas: This was the day—the day the packaging industry awaited with bated breath. GlobalPack Industries, one of the largest manufacturers of packaging materials, opened a brand new state-of-the-art facility in Houston, Texas, for the manufacture of PVC film especially intended for use in blister packaging. Among those present at the launch were key figures from the industry, local government authorities, and company bosses. This marked a significant step in production capacity expansion for GlobalPack. Key People Present The event was spearheaded by GlobalPack CEO, Emily Carter, who was flanked by Texas Governor, Jake Martinez, and Houston Mayor, Maria Hernandez. The representatives were from the pharmaceutical, electronics, and consumer goods industries, signaling that this new facility would indeed affect a wide array of sectors. Reasons for Expanding This increase in production was based on a steep rise in demand for PVC film in blister packaging. The COVID-19 pandemic brought higher demands on safe and tamper-evident packaging, notably from the pharmaceutical industry. Substantially relying on the blister packs in medication protection and dispensing, their demands surged. Moreover, consumer electronics adds to pressures on existing capacities with protective packaging. According to Emily Carter, "Our customers need trustworthy, high-quality PVC film for their packaging solutions. This new facility is the direct response to those needs, ensuring that we can answer the growing demand without ever compromising our commitment to sustainability and innovation." The Manufacturing Process The facility in Houston represents a cutting-edge plant capable of producing PVC film of high quality to meet the stringent requirements for blister packaging. It starts polymerizing vinyl chloride monomers into PVC resin and then extrudes and biaxially orients the film. State-of-the-art machines equipped in this facility are able to produce film with well-controlled thickness and surface properties to meet all customer-specific needs. The facility is also designed with sustainability in mind. Energy-efficient processes and recycling of industrial waste are integrated in the facility in order to minimize its impact on the environment. "We invested in technology that would make a better product but would also lower our carbon footprint," said Carter during the launch. Results of the Expansion A new facility in Houston will increase GlobalPack's PVC film production capacity by 40%. This means significantly reduced lead times to any customer located anywhere in North America. This will also mean the creation of more than 200 new jobs within the Houston area, providing a boost to the local economy. This first batch of PVC film from the new facility is due to be shipped to major pharmaceutical and electronics manufacturers by the end of September 2023. Initial tests indicate that the film is well within industry standards in terms of clarity, durability, and resistance to chemicals, and can thus be used in a large variety of blister packaging applications. Industry Effects The opening of GlobalPack's new facility is likely to create a chain reaction within the packaging industry. With more volumes of high-quality PVC film made available, it raises the performance and reliability standards for blister packaging—thereby motivating further innovation in this direction for packaging design, particularly for where safety and tamper evidence come first. The facility will most likely set a new standard within the industry toward sustainability and push other manufacturers to be greener. "This is more than just an expansion; it's a commitment to the future of packaging," said Carter. Conclusion GlobalPack once again leads the way in the packaging industry with the launch of a new PVC film production facility in Houston. With increased capacity in production, attention to sustainability, and the creation of new jobs, it is sure to meet the growing demands of various industries for high-quality blister packaging solutions. As the first shipments come out over the coming weeks, the ripples of this growth will be felt throughout the supply chain, further entrenching GlobalPack's position as a leader in the packaging industry.
Title: Pharmaceutical Company Launches New Thermoformed PS Film Packaging to Enhance Product Safety Date: August 15, 2023 Location: Basel, Switzerland In a groundbreaking move for the pharmaceutical industry, Swiss-based pharmaceutical giant, MediPharm, has announced the launch of its latest packaging innovation—thermoformed polystyrene (PS) film packaging. The new packaging solution was unveiled at a press conference held at MediPharm's headquarters in Basel, where company executives highlighted the advantages and future implications of this development for the industry. Key People Involved: The announcement was led by MediPharm's CEO, Dr. Andreas Müller, and the Head of Packaging Development, Dr. Elena Weiss. Both have been instrumental in driving the project from concept to implementation. Also in attendance were representatives from the company’s manufacturing partners and key stakeholders in the pharmaceutical supply chain. Causes and Motivations: The initiative to develop thermoformed PS film packaging stemmed from MediPharm's commitment to enhancing the safety and integrity of its pharmaceutical products. In recent years, the company has faced challenges with existing packaging materials that, while effective, did not fully meet the evolving needs of the market, particularly regarding durability, product visibility, and cost efficiency. Additionally, the rising concern for product safety during transportation and storage pushed the company to seek out a more robust packaging solution. Development Process: The development of the new PS film packaging began two years ago, with MediPharm's R&D team conducting extensive research into various materials and packaging technologies. The team focused on identifying a material that could offer superior protection against environmental factors, maintain the integrity of sensitive medications, and be easily customizable for different pharmaceutical products. After rigorous testing and several iterations, the team settled on polystyrene (PS) films due to their clarity, rigidity, and excellent thermoforming capabilities. Collaborating with leading packaging manufacturers, MediPharm developed a production process that utilizes advanced thermoforming techniques to create custom-fit packaging for various pharmaceutical products, including blister packs, trays, and clamshells. Results of the Launch: The introduction of thermoformed PS film packaging has been met with positive responses from industry experts and partners. Dr. Elena Weiss highlighted that the new packaging not only enhances the protection of the products but also significantly improves the efficiency of the packaging process. “We’ve seen a 20% reduction in material costs and a 15% increase in production speed, thanks to the lightweight and easily moldable nature of PS films,” Dr. Weiss reported. Moreover, the clear visibility offered by PS films has been praised for its potential to reduce errors in product identification and enhance quality control. The launch also aligns with MediPharm’s sustainability goals, as the new packaging material is fully recyclable, addressing concerns about environmental impact. Effects and Future Implications: The successful rollout of thermoformed PS film packaging is expected to set a new standard in pharmaceutical packaging. MediPharm plans to extend the use of this packaging across its entire product line within the next year, with the potential for collaboration with other pharmaceutical companies seeking to adopt similar technologies. Dr. Andreas Müller expressed confidence that this innovation would not only improve the safety and efficiency of MediPharm's products but also drive positive change across the pharmaceutical industry. “We believe this new packaging will lead to greater confidence among consumers and healthcare providers in the safety and reliability of our products,” Dr. Müller stated. As the industry continues to prioritize product safety and sustainability, MediPharm’s introduction of thermoformed PS film packaging could mark a significant shift in how pharmaceutical products are packaged and delivered to the market.
Title: PP Film Revolutionizes Printable Materials Market Date: August 15, 2023 Location: New York City, NY Key Figures: John Carter, CEO of PrintTech Solutions, and Dr. Emily Roberts, Lead Researcher, Advanced Polymers Lab Event Overview: Although PP film has been a recent spotlight in printing, diverse applications make it an ideal material for various uses. On August 15, 2024, the company leading developments in printable materials, PrintTech Solutions, held a press conference in New York City to introduce their most current innovations in PP film technology. Background: This film is also in great demand in the printing area because of its unique features like flexibility, durability, and lower costs. Unlike other printing material, traditional printing PP film will provide a non-porous, smooth surface for high-quality printing of vivid colors and sharp details. With such properties, it finds greater application in labels, packages, banners, and several other printed material types. According to John Carter, chief executive of PrintTech Solutions, demand for sustainable, high-performance printing materials is growing fast. "As companies look at reducing their environmental footprint while maintaining the highest level of quality, PP film becomes the material of choice in a broadening range of applications," he added. Development Process: According to Dr. Emily Roberts, lead researcher of the Advanced Polymers Laboratory, several breakthroughs in science have made the development of advanced PP films possible. She further elaborates on the research orientation: "In our team, we had focused on the improvement of the printability of PP film by adjusting its surface properties and improving its compatibility with flexographic, digital, and screen printing technologies.". The team has also worked on enhancing its resistance to fading so that the film retains the brilliance of the printed matter, even when exposed to blinding sunlight for a longer period and harsh environmental conditions. Result and Impact: The result of these innovations is a new line of PP films that are more durable, flexible, and increasingly environment-friendly. PP films developed by PrintTech Solutions are fully recyclable and produced with a lower carbon footprint compared to traditional materials, in line with the growing consumer demand for sustainable products and the industry's move toward eco-friendly practices. These advanced PP films, therefore, within the very short time of their introduction, have brought tremendous change in the printing industry. Some big houses have started using the material for their packaging and promotional material and commented positively about the superior print quality, durability, and sustainability. Moreover, it is cost-effective and also turned out to be very impressive for a business venture by cutting down costs without affecting the quality. Conclusion: The importance of PP film in the future will only continue to rise with the further expansion of the market in printable materials. Companies at the forefront of such developments are those like PrintTech Solutions, and leading educational research institutions like Advanced Polymers Lab; PP film will soon become a benchmark within the industry for quality and sustainability in printing. Their success is just another indication of the growing requirement for materials that can answer both performance and environmental demands, setting a new benchmark for the future of printable materials.
An application of the BPET conductive material boosts the electronics industry. August 2024, Shanghai, Global Electronics Manufacturing Exhibition; Zhang Qiang: technical director of a leading electronics materials R&D company. In August 2024, at the Global Electronics Manufacturing Exhibition held in Shanghai, a new type of conductive material took center stage. The Technical Director, Zhang Qiang, of one of the key Electronics Materials R&D enterprises, has brought along with him a team to introduce very latest BPET (Biaxially Oriented Polyethylene Terephthalate) conductive material. This launch marks the large step forward applying static protection and conductive materials within the electronics industry. Background: Help Needed to Meet Increased Demand for Static Protection With their ever-growing sophistication and complication, electronic products are also requiring more dependable static protection and conductive materials. Having noticed this emerging market demand, Zhang Qiang and his group embarked on a multi-year development program in search of creating a high-performance material to satisfy the demand. "We all noticed that all kinds of conductive materials available in the market had a number of problems, such as low transparency and unstable conductivity, which limited their usage in high-end electronic devices," Zhang Qiang explained during the launch. "It is this that moved us to develop a material that links high transparency, brightness, and stable conductive performance to serve the industry much better." Process: Overcoming Technical Challenges and Enhancing Performance The BPET material is produced with the help of imported production lines to ensure high transparency, brightness, and crystal-free surfaces with excellent flatness. Food grade slip agents were added by the team into the material to give it excellent surface smoothness, good processability, and well-preserved conductive properties. BPET sheets come in various specifications, thereby allowing for high production capacity at superior quality and cost-effectiveness. This is an environment-friendly and non-toxic material that meets QS food safety certification and passes the European Union's SGS environmental certification, hence suitable for industries with strict compliance criteria to safety and the environment. The following are several conductive grades for the materials: - Permanent Conductive Sheet: $10^10$ ohms - Permanent Antistatic Sheet: 10^10 ohms - Permanent Semi-Conductive Sheet: 10^6-10^9 ohms These variations show steady and smooth conductive performance, which ensures the stability and reliability of products for various applications. Besides, BPET can be processed into flat sheets, slit, and laminated; while PET-G and GAG grades are especially suitable for producing high-end electronic products. Result: Good Market Response and Wide Industrial Application In the exhibition, BPET conductive material was very fast.
Revolutionizing Folded Box and Pharmaceutical Thermoforming Packaging—PVC Sheets Date: August 13, 2023 Location: Shanghai, China Key Players: Leading packing manufacturers, pharmaceutical companies, environmental advocates Event Summary: In what could emerge as the most radical paradigm shift in packaging, Shanghai's top manufacturers yesterday announced increased application of polyvinyl chloride sheets for folded box and pharmaceutical thermoforming packaging. This will change the world in terms of product protection, cost efficiency, and manufacturing versatility. Background: Durability, flexibility, and cost represent some of the most preferred characteristics of PVC, and it has thereby found a place in most industries. However, recent developments in manufacturing PVC sheets raise renewed interest in using the material for special applications in pharmaceutical packaging and other consumer products. Cause and Course of Events: The trend of using PVC sheets in folded box and pharmaceutical packaging started this year when a number of packaging specialists, associated with different pharmaceutical companies, launched an all-inclusive study regarding the effectiveness of the material. Their conclusions, published in June 2024, pointed to some main advantages of PVC sheets, first of all related to their better defense against moisture, oxygen, and light—parameters that play a very important role in the preservation of pharmaceutical products. After the research, some leading packaging companies in Shanghai started to apply PVC sheets in their production lines within a very short period of time. It is the possibility of easily cutting, folding, and thermoforming the material into desired shapes that allows these companies to fulfill the tough requirements from pharmaceutical industries while offering beautiful and functional packaging to consumer products. Result: Beginning with the adoption of PVC sheets, fruitful results have already started to show. Pharmaceutical firms are reportedly found to declare that most of the problems related to packaging, such as contamination and damage of the product during transportation, have reduced considerably. Consumers have also welcomed the enhanced protection and longer shelf life of products packaged with PVC. Moreover, this reduces the overall production cost of PVC sheets, thereby enabling the manufacturer to maintain a competitive price and upgrade the quality of packaging. Impact and Future Prospects: Interest in PVC sheets for folded box and pharmaceutical thermoforming packaging has been quite successful, and other markets, like food and electronics, where solid, protective, and cost-efficient packaging is a must, may get attracted to it. Environmentalists still are wary and remind that without recycling programs, harm to the environment from PVC will only continue to grow. As innovations further the development in the packaging industry, PVC sheets can only play an ever-increasing role as a solution providing a reliable performance-cost-consumer safety balance for manufacturers. With Shanghai at the helm of this change, its packaging sector is well on course to lead global efforts towards improving products' packaging through strategic material use, such as PVC.
Polycarbonate Sheets Revolutionize Light Diffusion: A Breakthrough in Modern Lighting Solutions Date: August 12, 2024 Location: Shenzhen, China Key Figures: Dr. Li Wei, Senior Researcher at Shenzhen Lighting Technologies; Zhao Ling, Chief Product Officer at BrightLight Innovations Shenzhen, China - In a groundbreaking development for the lighting industry, polycarbonate (PC) sheets have emerged as the leading material for light diffusion applications, thanks to their superior performance and versatility. This breakthrough was announced today at the Shenzhen International Lighting Expo, where Dr. Li Wei, a senior researcher at Shenzhen Lighting Technologies, and Zhao Ling, the Chief Product Officer at BrightLight Innovations, presented the latest research and product developments utilizing PC sheets. The Problem: Seeking the Perfect Light Diffuser The need for efficient and aesthetically pleasing lighting has been a persistent challenge across various industries, from commercial and residential lighting to automotive and architectural applications. Traditional materials used for light diffusion, such as acrylic or glass, have often fallen short in terms of durability, weight, and optical performance. These limitations have driven researchers and manufacturers to explore alternative materials that can deliver consistent, high-quality light diffusion while meeting the rigorous demands of modern applications. The Breakthrough: Why Polycarbonate Sheets? Polycarbonate sheets have long been known for their impact resistance, clarity, and lightweight properties. However, their application as light diffusers has only recently been fully realized, thanks to advancements in material science and processing techniques. During the expo, Dr. Li Wei explained how PC sheets are engineered to achieve optimal light diffusion while maintaining high transparency and strength. "Polycarbonate sheets offer a unique combination of properties that make them ideal for light diffusion," said Dr. Li. "Their inherent ability to scatter light evenly without significant loss of brightness sets them apart from other materials. Additionally, the durability of PC ensures that the diffusers remain effective over time, even in harsh environments." The Process: Development and Testing The journey to this breakthrough began two years ago when Shenzhen Lighting Technologies partnered with BrightLight Innovations to develop a new generation of light diffusers for various lighting applications. The team, led by Dr. Li and Zhao Ling, conducted extensive research and testing to refine the material properties of PC sheets. Through a series of laboratory tests and field trials, the team discovered that PC sheets could be engineered to diffuse light evenly while maintaining a high level of transparency. This was achieved by carefully controlling the thickness and surface texture of the sheets, allowing them to scatter light effectively across a wide area. "We focused on optimizing the material to meet the specific needs of our clients," Zhao Ling explained. "Whether it's for automotive headlights, architectural lighting, or LED panel lights, our PC-based diffusers provide unmatched performance in terms of light quality and durability." The Result: A New Standard in Lighting The introduction of PC sheets as light diffusers has already begun to transform the industry. Several major lighting manufacturers have adopted this technology, citing improved light quality, reduced glare, and increased energy efficiency as key benefits. In addition, the lightweight nature of PC sheets has made them easier to handle and install, further enhancing their appeal in large-scale projects. At the expo, attendees had the opportunity to see the results firsthand, with several demonstrations showcasing the effectiveness of PC sheets in various lighting applications. The response from industry professionals has been overwhelmingly positive, with many expressing interest in integrating PC-based diffusers into their product lines. The Future: Expanding Applications Looking ahead, both Shenzhen Lighting Technologies and BrightLight Innovations plan to continue their collaboration to explore new applications for PC sheets in light diffusion. The companies are already working on the next generation of products that will push the boundaries of what's possible in lighting design. "We believe that this is just the beginning," said Zhao Ling. "The versatility of polycarbonate sheets opens up endless possibilities for innovation in lighting. We're excited to see where this technology will take us next." Conclusion The successful application of polycarbonate sheets in light diffusion represents a significant advancement in the field of lighting. By offering a superior alternative to traditional materials, PC sheets are poised to become the new standard in creating high-quality, durable, and energy-efficient lighting solutions. As this technology continues to evolve, it promises to bring even more innovation to the industry, benefiting both manufacturers and consumers alike.
The Rise of PET Sheets in Food Packaging and Labeling: A Sustainable Choice *Date: August 9, 2023 Location: Global Market Key Stakeholders: PET Manufacturers, Food Industry, Environmental Organizations* Introduction Polyethylene Terephthalate (PET) sheets have rapidly gained traction in recent years as an innovative material in the packaging industry. Renowned for their excellent toughness, high strength, and superior transparency, PET sheets have become a favored choice for food packaging and labeling applications. The material’s ability to be printed on, recycled, and its environmentally friendly properties, particularly its non-toxic combustion process, have further solidified its position as a leading packaging solution. This article explores how PET sheets are transforming the food packaging and labeling landscape, highlighting key developments and their impact on the market. Background PET sheets were developed to address the growing demand for materials that not only provide strong protective packaging but also align with global environmental sustainability goals. With the increasing awareness and concern over environmental degradation, particularly from non-recyclable plastics, the food industry began searching for alternatives that could offer both functionality and eco-friendliness. PET sheets, with their remarkable features, emerged as an ideal solution, gradually gaining popularity among consumers, producers, and environmental advocates alike. Features and Advantages 1. Transparency and Gloss: PET sheets offer exceptional transparency and surface gloss, making them highly effective in showcasing food products. This feature is especially valuable in retail environments, where product visibility is a critical factor in consumer decision-making. 2. Surface Decoration: The surface of PET sheets is highly receptive to decoration without the need for additional surface treatments. They are easy to print on, emboss, and even metalize using vacuum metal coating, making them ideal for creating attractive and informative labels. 3. Mechanical Strength: The robust mechanical strength of PET sheets ensures that food products are well-protected during transportation and handling, reducing the risk of damage and spoilage. 4. Barrier Properties: PET’s excellent barrier properties against oxygen and water vapor help preserve the freshness and quality of food products, extending their shelf life. 5. Chemical Resistance: PET sheets are resistant to various chemicals, which is crucial for packaging foods that may come into contact with reactive substances. 6. Safety and Hygiene: Non-toxic and compliant with stringent hygiene standards (such as GB13113-91), PET sheets are suitable for packaging food, pharmaceuticals, and medical devices. They can also be sterilized using radiation, ensuring the safety and integrity of the packaged goods. 7. Environmental Compatibility: PET is not only recyclable but also burns without releasing harmful substances, making it a key material in the global push for sustainable packaging solutions. Its excellent thermoforming capabilities allow it to be easily molded into various shapes, further enhancing its versatility in packaging applications. Event and Impact In recent years, several leading food manufacturers have transitioned to using PET sheets for their packaging and labeling needs. This shift was primarily driven by the material’s superior performance and environmental benefits. For instance, in a significant move in 2023, a global food giant replaced its traditional PVC packaging with PET for its entire line of snack products. This decision was lauded by environmental groups and resulted in a notable increase in sales, as consumers responded positively to the company’s commitment to sustainability. Moreover, the adoption of PET sheets in labeling has revolutionized the way food products are presented and marketed. The ability to easily print high-quality graphics and text directly onto the packaging has enabled brands to create more engaging and informative labels, enhancing their appeal on store shelves. Outcome and Future Prospects The widespread adoption of PET sheets in food packaging and labeling has led to a significant reduction in the environmental footprint of the packaging industry. The material’s recyclability and safe combustion have addressed many of the environmental concerns associated with traditional packaging materials. As a result, PET sheets have not only met the immediate needs of the food industry but also contributed to the long-term goal of reducing plastic waste and promoting sustainability. Looking ahead, the market for PET sheets is expected to continue growing, with more industries recognizing their value. Ongoing advancements in PET technology, such as improved barrier properties and enhanced printability, will likely further solidify PET’s position as the material of choice for food packaging and labeling. In an era where environmental sustainability is no longer an option but a necessity, PET sheets are set to play a pivotal role in shaping the future of packaging.
Polystyrene in Seedling Trays and Food Containers: An Overview of its Role Date: 8th August 2023 Location: Global Key Figures: Environmentalists, Industry Experts, Policymakers Introduction 8th August 2024 is the day that saw a heated, highly perceived argument of the use of Polystyrene commonly abbreviated as PS in the making of growing seedling trays and food containers. The debate borders on the balance between the practical usefulness of PS and its effect on the surrounding environment. Background Sand used to be the raw material for the production of polystyrene, which is a very wide applied plastic because of its cost-effectiveness and versatility in application. In horticulture, PS is used for seedling trays so that they can give their supporting plant effective drainage and serve a longer time due to their strength. In the food service sector, PS is used for containers like clamshells and cups due to its insulative and affordable properties. Events Horticulture Sector: Environmentalists in the previous decades have already raised concern on the future environmental impacts of PS seedling trays. Although the trays are durable and even to some extent, are reusable, these trays still add to plastic pollution because they are non-biodegradable. Other areas have already explored alternative materials to reduce plastic waste on gardening refuse. Food Service Sector In the same vein, the food service sector has been pressured by the public to discontinue its heavy use of PS containers. While the reasons behind this popularity are insulation and cost reduction, they have been faulted for contributing to the volume of landfill sites and being potential health risks. Recent reports have shown the need to shift to biodegradable packaging systems. Findings Plan Response from Industry: Going Green. In response to these perceptions, the horticulture and food service industries have began to react to the environmental impact of PS. These key steps include, 1. Alternatives: Research over biodegradable and compostable alternatives has been expedited. Industries now look into materials like plant based plastics and recycled fibers that can substitute common PS. 2. Developed Recycling Programs: Advanced recycling infrastructure is developed to manage a better waste load from PS. Developed recycling technologies and programs are being introduced to recover and reutilize materials made from PS. 3. Policy Change: Many countries' governments have framed regulations to control and limit the use of PS in single-use products. The policies have been framed to promote and encourage the use of sustainable alternatives and improve the management of waste. Impact And, the following are some of the positive impacts that the global response to the PS issues resulted in: Increased Awareness: Increased awareness among consumers and industry-related people about the environmental effects of PS and their role has facilitated informed choices and practices. Developing New Materials: The search and, to a contrary, immediate need for alternative sustainable gear had resulted in developing new eco-friendly types of materials in place of the traditional PS used in the nursery trays and food containers. - Advancements in Policies and Regulations: New policies and regulations enable changes toward sustainable operations directed to horticulture and foodservice sectors. Conclusion The ongoing discussion of the role of Polystyrene in seedling trays and food containers really brings the point of balancing practical advantages with environmental responsibility. The work on these challenges has been attended to, in developing partnership with industry and government, while the focus is on sustainability and being innovative with the future of eco-friendliness in both gardening and food service.
PC Sheets: Revolutionizing the Construction of Sunrooms New York City, August 7, 2023: New sunroom construction and other transparent structures are using a new generation of polycarbonate (PC) sheets above 1.0 millimeters in thickness to take a technological leap forward. Renowned for its resistance to wear and tear and wide-ranging uses, these PC sheets prove to be the most sought after by architects and constructors. The Key Features of PC Sheets 1. Impact Resistance: The PC sheets are highly resistant to impact; that is, sunrooms can also be built to withstand harsh weather conditions like hailstorms and other such wind storms. This has just been proved recently by architect Emily Johnson, who was leading a project for the construction of a new sunroom in Brooklyn. "The durability of PC sheets gives us the confidence to design structures that can endure extreme weather," Johnson stated. 2. Scratch Resistance: A PC sheet has little possibility of getting scratched, thus keeping the clarity and looks for years. It was a salient feature when construction manager John Adams took on the renovation of a historical greenhouse in Central Park. "With scratch-resistant properties, the PC sheet works wonders to keep the greenhouse looking good over the years," said Adams. 3. Antistatic Properties: Dust does not settle on PC sheets and hence reduces the maintenance burden. This was especially of value to the creation of a new botanical garden in Queens. According to Laura Green, the project manager, "The antistatic properties allow the structure to stay clean and clear of dust, improving the experience of visitors." 4. Waterproof and Leak-Proof: PC sheets are impermeable to water; hence, they are appropriate for structures that undergo the rainfall and moistening processes. Contractor Michael Lee used such sheets in a current project in Miami to build a sunroom that was waterproof. "The leak-proof nature of PC sheets protects the structure from water damage, ensuring longevity," Lee explained. 5. Resistance to Corrosion: PC sheets show very excellent resistance to a large number of chemicals and thus are appropriate for use in outdoor applications. For instance, an oceanfront sunroom was constructed recently in Malibu, and environmental consultant Sarah Davis applauded the fact that the sheet did not corrode under salty air and other corrosive elements. "PC sheets' resistance to corrosion is one major advantage in coastal regions," said Davis. 6. Aging Resistance: These sheets are resistant to yellowing or degradation even under the most extended exposure to sunlight. This had been showcased in a recent project at Phoenix where urban planner David Wilson had used these PC sheets in designing a public sunroom. "The aging resistance ensures that the sunroom retains its clear and attractive appearance for many years," said Wilson. 7. High Flame Retardancy: Flame-retardant properties increase safety. At a safety demonstration in Chicago recently, firefighter Mark Thompson gave a fine illustration of how PC sheets would prevent the spread of fire in residential sunrooms. "Flame retardancy of PC sheets is the key to save lives and property," said Thompson. 8. Custom Finishes: The PC sheets can be finished in different colors and coatings to give more aesthetic flexibility. One vividly colorful project in San Francisco, an addition of a sunroom, was accomplished using the said colored PC sheets. "The possibility of custom finishes of PC sheets is just endless design possibilities," said Roberts, a designer. 9. High-Temperature Thermoforming: The sheets are easily molded into complex shapes and versatile in terms of designing applications. This was evident in the recent innovative project in Denver where engineer James Baker used the sheets to make uniquely shaped sunroom panels. "The high-temperature thermoforming capability of the PC sheets allows creative and intricate designs," said Baker. Conclusion The introduction of PC sheets over 1.0 mm thick changed everything in sunrooms and generally all transparent buildings. Their impact resistance, scratch resistance, antistatic properties, waterproofing, resistance to corrosion, aging, flame retardancy, and the possibility of thermoforming with various finishes set a new standard in the industry. As more architects, designers, and contractors begin to use these versatile sheets, the future of sunroom construction is about to shine brighter and get more creative than it has ever been.