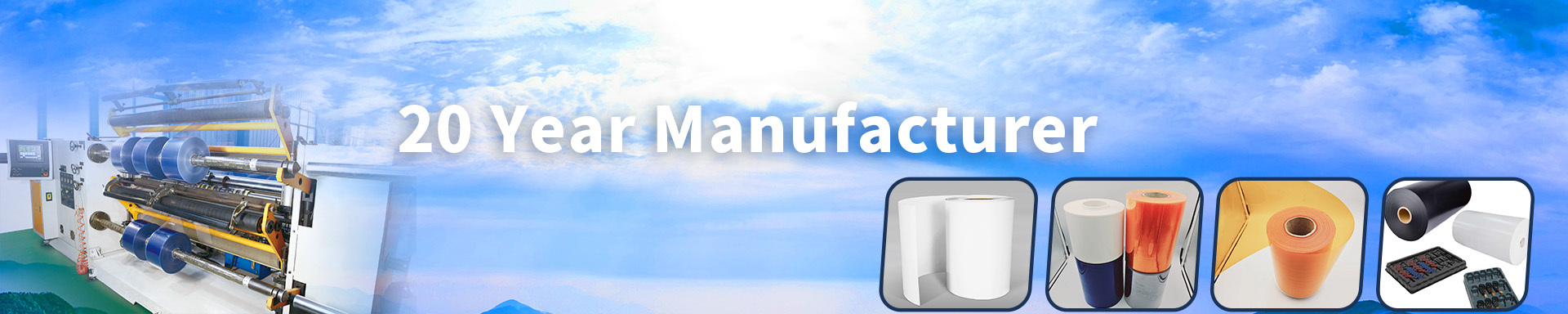
- Home
- >
News
Transparent PET film is a versatile material with a wide range of applications in different fields. Its unique properties, such as transparency, durability, and barrier properties, make it an ideal choice for many applications. Whether it is used for insulation, packaging, decoration, or healthcare, PET film plays an important role in our lives.
1. Advertising and Signage Printable transparent PVC film is widely used in the advertising and signage industry. Its transparency allows for creative designs that can be applied to windows, glass doors, and other transparent surfaces. Whether it's for promoting a brand, announcing an event, or providing directional signage, PVC film offers a sleek and eye-catching solution. The film can be printed with vibrant colors and high-resolution graphics, ensuring maximum visibility and impact. For example, in retail stores, printable PVC film is used to create window displays that attract customers and showcase products. The transparency of the film allows passersby to see inside the store while still being able to view the promotional messages printed on the film. In addition, PVC film can be used for outdoor signage, such as billboards and banners, as it is weather-resistant and can withstand exposure to sunlight, rain, and wind.
Antistatic and Thermoformable PET Film: Wonders of Versatility by In the bustling metropolis, one young, innovative entrepreneur named Lily Chang was going to change the world of materials. It was the year 2024, and Lily had just discovered the astonishing properties of antistatic and thermoformable PET film. Little did she know that this would be an exciting journey that would affect many industries and change lives. The finding of sustainable and practical solutions for day-to-day problems had always remained close to her heart. Progressing further in the world of materials, she found anti-static thermoformable PET film. Curious about its capabilities, she started to find ways where it can be used. It was on one such day while sitting in the small office and gazing out at the skyline of the city that she finally thought that with such film, she might print out A4 sheets that are singularly special. She was so thrilled by the very idea that soon she got down to work on it. Lily then called a local printing company and described her idea. To begin with, the printing company was somewhat skeptical, but once they had samples of the PET film, skepticism turned into interest. Together they began experimenting with different ways of printing the film and soon discovered that it could bear excellent bright prints. The news began to circulate about Lily's printable A4 PET film sheets. Their unique features increased the attraction of students and professionals alike towards these sheets. Because of the antistatic property, prints do not possess static electricity and hence are easily handleable and storable. The thermoformable nature of the film opens more ways of creative usage, such as making note cards or bookmarks in an arbitrary form. As the news spread, Lily was invited to present the product at a local trade show. She was happy to expose her innovation to more people, so she accepted the invitation. The booth was flooded with visitors during the trade show. Still, people were further surprised to see the versatility of PET film. One of them was Alex, a graphic designer who was pretty impressed and visualized using these sheets for his design projects. Alex walked up to Lily and started a conversation with her. Soon, both found that they shared an interest in innovation and design. Alex also mentioned to her about the PET film for customized packaging and how she could join on a project to work with it. The idea thrilled Lily, and they did not delay in starting their work. They started researching all types of packaging needs and came up with a few ideas. One of the ideas was to do some innovative packaging for a local cosmetics brand. The cosmetic company was looking for varnish and striking green packaging solutions. Lily and Alex presented their idea of using antistatic and thermoformable PET film. Interested, the company decided to give it a try. Thus, Lily and Alex were putting great effort into designing packaging and then actually making it. They used the thermoformable property of the film to create custom shapes that would fit the cosmetics products perfectly. The antistatic feature would protect them against electrostatic discharges during transport and storage. The result was amazing. The packaging was beautiful, but not only that-it was functional. It called the attention of the consumers and soon became a hit. The cosmetics company loved the result and ordered more of such packaging. Buoyed by the success, Lily and Alex continued to explore other applications of the PET film. They soon turned their attention to food and pharmaceutical industries. Safety and freshness are key factors in the food industry. Lily and Alex realized that the antistatic and thermoformable PET film would assist in maintaining the freshness of the food and containing no contaminants. They had a package designed with the local food manufacturer for his products. This proved ideal for properties such as packaging of food. Antistatic dispensers prohibited the adherence of dust and other particles onto the packagings, while the thermoformable property allowed customized shapes, which fit different food items. In this case, this turned out to be effective yet attractive packaging. The pharmaceutical industry demands sterile and safe packaging. Lily and Alex worked with a pharmaceutical company to develop packaging that would meet these demands. The PET film instantiated an antistatic property of the film which prevented the build-up of the charges capable of damaging some sensitive medications. The thermoformability was adjustable for those custom-designed packaging meant to secure the drugs during transportation and storage. Here, both Lily and Alex had a reason to look forward to further opportunities once their projects were successful in food and pharmaceuticals producing industries. As a matter of fact, they were invited as guest speakers in industry conferences where they shared their experiences with others. As they got more and more popular, one day, Lily and Alex were approached by a local interior designer. The interior designer wanted something very special for his next big decoration project. Lily and Alex recommended the PET film. They worked with designers for the creation of custom walls and decorative panels. The thermoformability of the film allowed for creative designs and figures, along with an antistatic feature of the decorations, which made them without static electric properties, thus giving an amazing look of space. In the field of glass decoration, Lily and Alex also carved their niche. They also developed a method of applying the PET film to glass surfaces to make privacy screens, decorative windows, and other unique glass features. Because of the properties of this film, installation and removal were pretty easy; thus, it found its place in residential and commercial usages. As the year drew to a close, Lily and Alex looked back with pride to see how it had been. They had taken an easily available material and molded it into a multiutility solution making a difference in various industries. From printable A4 sheets to creative packaging, decoration items, up to glass enhancement, the list of applications for thermoformable PET film is endless. Their story of Lily and Alex had emphasized the force of innovation and teamwork. They had proved that with just a little creativity and determination, even one simple material could go a long way into changing the world. They knew that their journey of thermoformable and antistatic PET film was far from over as they looked to the future. Actually, they were pretty excited about the new applications of the material and the new opportunities. Conclusion: This is quite a remarkable story involving discovery and use of antistatic and thermoformable PET film by Lily Chang and Alex. It's reached into printing and packaging, food, pharmaceuticals, decoration, and the decoration of glass. Their traits have proven-you just need to think differently, and you will definitely find something which is suitable and applicable in everyday industrial problems. With ever-growing sustainability concerns and the need for versatile materials, antistatic, and thermoformable PET film possibly holds a bright future for any who would dare to work and venture into it.
Anti-Static, Thermoformable PVC Film—Emerging Use One fine morning of [date] in the hustling city of [city name], a young entrepreneur, Lily Zhang, demonstrated the amazing versatility of the anti-static, thermoformable PVC film. Since she was a child, Lily was always interested in finding creative solutions for packaging and decoration problems. The first interest in PVC film came when she realized the growing needs for materials that combine functionality and aesthetics. Only the good and careful investigation of this topic, along with the examination, have greatly nurtured this interest, leading to the exploration of the peculiar features of anti-static thermoformable PVC film. At the beginning of this story, Lily visited a local packaging factory. Sensitive electronic parts, being packaged at this factory, would be destroyed by the static electricity. Their acquaintance was made with anti-static PVC film. The ability of the film to dissipate static charge caught immediate attention with the managers of this factory, which decided to give it a try. The PVC film was put on at the packaging stage, and Lily did it with the help of the factory team. The result was that the problem of static electricity disappeared, and the products packed could not be damaged in any way. Improved packaging gave a nicer look to the products, which was more catching for the customers. Not content with this single success, Lily applied her mind to the food packaging industry. She knew the importance of safety and presentation of food. With an anti-static PVC film, she was in a position to offer a solution that would protect the food from static charge, besides offering a clear and hygienic method of packaging. She toured some food processing factories and could demonstrate to them the feasibility of the PVC film. The plant managers could not believe how durable the product was, and how clean it was to use. They bought into the product and were now using the film to package fresh fruits, fresh vegetables, and even processed snack foods. The food can now be transported and stored without going bad and contaminated by any foreign matter. Next was pharmaceutical packaging. The requirements were much tougher: sterile packaging that protected the drugs from moisture and static electricity, yet conformed very strictly with the rules. Lily's anti-static PVC film proved up to the task. She worked in cooperation with pharmaceutical companies for the development of special packaging solutions. Examples of packaging made from this film are pills, tablets, and liquid preparations. Because this material is thermoformable, the form and size of packaging are easily managed to precisely fit a product. Anti-static properties protect medication from static damage, while clarity of the film allows for the possibility of seeing through for quality control. In interior decoration, Lily has found a completely new domain of application for the PVC film. She conceived using it in making those really unique and eye-catching designs in the apartment. She went and started co-operating at first with interior designers, then architects. Together, they were creating such a thing as wall coverings, so-that ceiling paneling, some decorations. Consequently, the PVC film could be let loose with abandon. It could be embossed printed, several patterns and colors could be offered or mixed, thus providing the designer with an ample latitude in working on interiors that are very personalized and chic. It was also easy to install and maintain and for these reasons preferred, not only by households but business establishments as well. Yet, in the field of glass decoration, Lily's PVC film shone once again. She has also created the special adhesive-backed PVC film, which can be directly applied to the surface of glasses to add not only a decorative touch but also privacy and UV protection. The journey of Lily with the anti-static, thermoformable PVC film was not that smooth. She was rejected by convinced clients who would not easily convert to another material. But through her persistence and hard work, she was able to overcome these obstacles and prove the value of the PVC film. With the success of Lily getting announced everywhere, anti-static thermoformable PVC film began to contact more and more industries. For example, automotive interior and aerospace components, the application of it was burgeoning. Actually, Lily's innovation had really made a miracle in many fields. Today, Lily is regarded as one of the authorities in packaging as well as decoration material. And her case is used to inspire others who, in drastic means, seek solutions to their everyday troubles. Because of Lily's vision and insistence, antistatic thermoformable PVC film is now indispensable in many industries. This thermoformable film has found application within the fields of packaging, food packaging, pharmaceutical packaging, decoration, and glass decoration because of its anti-static property. Unique qualities and infinite creativity opened up new paths of innovation and invention. Behind this successful innovation stands Lily Zhang, a young entrepreneur who dared to dream and make a difference.
Revolutionary Advance in Pharmaceutical Blister Packaging with White PVDC August 22, 2022 The state-of-the-art research facility in [City Name] A consortium of leading experts and researchers from the pharmaceutical packaging industry, including Dr.jackson Dr dunail, and their dedicated teams. Initiation: In an era where the pharmaceutical industry is constantly evolving to meet the escalating demands for safe and effective medications, the quest for optimal packaging solutions has become more crucial than ever. The increasing complexity of drug formulations and the need for prolonged shelf stability have posed significant challenges. This led to a focused effort on exploring novel materials that could provide an uncompromising shield against the external elements, ensuring the integrity and potency of pharmaceuticals throughout their lifecycle. The journey began several years ago when a group of visionary scientists and engineers, driven by a passion for innovation and a commitment to patient safety, embarked on a mission to revolutionize the landscape of pharmaceutical packaging. Their initial research involved a comprehensive analysis of various materials, considering factors such as barrier properties, chemical compatibility, and cost-effectiveness. The team spent countless hours in the laboratory, conducting meticulous experiments and subjecting potential materials to rigorous testing regimens. They evaluated a wide range of polymers and composites, but none seemed to meet all the stringent requirements until they stumbled upon the potential of white PVDC. However, the road to success was not without obstacles. The material presented unique processing challenges that required the development of specialized manufacturing techniques. The researchers had to fine-tune the extrusion and molding processes to achieve the desired thickness, uniformity, and clarity of the PVDC sheets. Simultaneously, they conducted extensive stability studies to assess the interaction of the white PVDC with different drug formulations. This involved subjecting the packaged drugs to accelerated aging conditions, simulating various environmental factors such as humidity, temperature fluctuations, and exposure to light. Through meticulous monitoring and analysis of the drug's physical and chemical properties over time, they were able to demonstrate the superior protective capabilities of the white PVDC packaging. Collaborations with leading pharmaceutical companies also played a crucial role in the development process. Feedback from industry partners provided valuable insights into the practical challenges faced on the production floor and the specific needs of different drug products. This iterative process of research, development, and feedback refinement was key to optimizing the performance and suitability of the white PVDC packaging solution. After years of dedicated research and development, the fruits of their labor have finally borne fruit. The use of white PVDC in pharmaceutical blister packaging has emerged as a game-changer. The material's exceptional barrier properties effectively prevent the ingress of moisture and oxygen, minimizing the degradation of drugs and extending their shelf life significantly. Clinical trials and real-world case studies have demonstrated that medications packaged in white PVDC retain their potency and efficacy for longer periods, reducing the risk of spoilage and ensuring patients receive high-quality treatments. This not only translates to better healthcare outcomes but also has economic implications, as it reduces the frequency of drug recalls and waste. The success of white PVDC has sparked a wave of excitement within the industry. Pharmaceutical companies are now actively exploring the integration of this innovative packaging material into their product lines, and regulatory authorities are closely evaluating its safety and performance to establish appropriate guidelines. Looking ahead, the future seems bright for white PVDC in pharmaceutical packaging. Continued research and development efforts are underway to further enhance its properties and expand its application to a wider range of drug formulations. This breakthrough is not only a testament to the power of scientific innovation but also a promising step towards ensuring the global availability of safe and reliable medications.
Headline: Global Adoption of PP EVOH Film Revolutionizes Packaging Across Industries Date: August 22, 2024 Location: New York, NY Introduction: In a dramatic turn of events, PP EVOH film fast becomes the material of choice for thermoforming and blister packing in almost every industry—from food and pharmaceuticals to industrial uses—owing to the advanced and highly competent solution it offers through barrier performance and versatility. Key Characters: - John Harrison: GreenPack Industries' CEO and leading manufacturer of PP EVOH films. - Dr. Emily Roberts: The head of the Research and Development section at SafeSeal Pharmaceuticals. - Mark Davis: The senior operations manager at FreshFoods Packaging Solutions. - Global Packaging Consortium: A coalition of experts on packaging matters and industry leaders. Causes: Growing demand for sustainable, high-performance packaging has forced the move to PP EVOH film. Rising consumer awareness about food safety and pharmaceutical efficiency has forced manufacturers to look for materials that extend shelf life, durability, and environmental benefits. In view of emerging global supply chain challenges, the need for packaging with excellent barrier protection against oxygen, moisture, and other contaminants is increasingly important. Process: The application of PP EVOH film began in early 2023 when GreenPack Industries, under the business acumen of John Harrison, had invested in intensive research and development to improve the properties of this material. Their work paid off in introducing a new line of PP EVOH films specially designed for various industries. One of the first ones to have spotted the potential of this film in the pharmaceutical sector was Dr. Emily Roberts of SafeSeal Pharmaceuticals. Her team has done an exhaustive test on the potential of this film to protect medication from environmental factors, thereby opening it up for wide adoption in the blister packaging for drugs. About the same time, FreshFoods Packaging Solutions' Mark Davis had introduced a PP EVOH film for use with perishable food items that extended their shelf life by allowing its barrier properties to reduce food waste and enhance supply chain efficiency on their thermoforming lines. At the Global Packaging Consortium summit in New York, June 2024, experts and industry thought leaders debate the future of new packaging materials. PP EVOH film will be one of the key focuses; participants agree that this material can set new standards in packaging across a gamut of industries. Results: The introduction of PP EVOH film has massively advanced the field of packaging. In food processing, freshFoods Packaging Solutions recorded an added 20% shelf life to their products, hence less food wastage and customer satisfaction. SafeSeal Pharmaceuticals had product recalls reduced by 15% due to the improved protection qualities that the PP EVOH film offered over the products in its blister packs. On the industrial front, GreenPack Industries increased their market share by 30% due to surging demands for PP EVOH film across the globe. This success also fueled innovation in recycling technologies to come up with more sustainable packaging solutions. Effects: The extensive application of PP EVOH film has had a domino effect on various industries. From the angle of customers, they receive fresher food and are offered much safer pharmaceutical products. On the other hand, for manufacturers, while the cost goes down, efficiency rises. Actually, the success of PP EVOH film already made other companies look into developing similar high-performance materials that would surely further create innovations in the package sector. The environmental effect from packaging is lessened as more and more companies take up recyclable PP EVOH films, giving a realization to global sustainability. According to the Global Packaging Consortium, in 2025, PP EVOH film may prove to be the precedent for barrier packaging, seeing remarkable protection performance and environmental responsibility. Conclusion: With the packaging industry in continuous flow of evolution, PP EVOH film has emerged to be that one game-changing material best suited to both the modern consumer and manufacturer. Proving its benefits and gaining in popularity, this innovative film is sure to set a new trend in packaging standards worldwide.
Title: Pharmaceutical Company Launches New Thermoformed PS Film Packaging to Enhance Product Safety Date: August 15, 2023 Location: Basel, Switzerland In a groundbreaking move for the pharmaceutical industry, Swiss-based pharmaceutical giant, MediPharm, has announced the launch of its latest packaging innovation—thermoformed polystyrene (PS) film packaging. The new packaging solution was unveiled at a press conference held at MediPharm's headquarters in Basel, where company executives highlighted the advantages and future implications of this development for the industry. Key People Involved: The announcement was led by MediPharm's CEO, Dr. Andreas Müller, and the Head of Packaging Development, Dr. Elena Weiss. Both have been instrumental in driving the project from concept to implementation. Also in attendance were representatives from the company’s manufacturing partners and key stakeholders in the pharmaceutical supply chain. Causes and Motivations: The initiative to develop thermoformed PS film packaging stemmed from MediPharm's commitment to enhancing the safety and integrity of its pharmaceutical products. In recent years, the company has faced challenges with existing packaging materials that, while effective, did not fully meet the evolving needs of the market, particularly regarding durability, product visibility, and cost efficiency. Additionally, the rising concern for product safety during transportation and storage pushed the company to seek out a more robust packaging solution. Development Process: The development of the new PS film packaging began two years ago, with MediPharm's R&D team conducting extensive research into various materials and packaging technologies. The team focused on identifying a material that could offer superior protection against environmental factors, maintain the integrity of sensitive medications, and be easily customizable for different pharmaceutical products. After rigorous testing and several iterations, the team settled on polystyrene (PS) films due to their clarity, rigidity, and excellent thermoforming capabilities. Collaborating with leading packaging manufacturers, MediPharm developed a production process that utilizes advanced thermoforming techniques to create custom-fit packaging for various pharmaceutical products, including blister packs, trays, and clamshells. Results of the Launch: The introduction of thermoformed PS film packaging has been met with positive responses from industry experts and partners. Dr. Elena Weiss highlighted that the new packaging not only enhances the protection of the products but also significantly improves the efficiency of the packaging process. “We’ve seen a 20% reduction in material costs and a 15% increase in production speed, thanks to the lightweight and easily moldable nature of PS films,” Dr. Weiss reported. Moreover, the clear visibility offered by PS films has been praised for its potential to reduce errors in product identification and enhance quality control. The launch also aligns with MediPharm’s sustainability goals, as the new packaging material is fully recyclable, addressing concerns about environmental impact. Effects and Future Implications: The successful rollout of thermoformed PS film packaging is expected to set a new standard in pharmaceutical packaging. MediPharm plans to extend the use of this packaging across its entire product line within the next year, with the potential for collaboration with other pharmaceutical companies seeking to adopt similar technologies. Dr. Andreas Müller expressed confidence that this innovation would not only improve the safety and efficiency of MediPharm's products but also drive positive change across the pharmaceutical industry. “We believe this new packaging will lead to greater confidence among consumers and healthcare providers in the safety and reliability of our products,” Dr. Müller stated. As the industry continues to prioritize product safety and sustainability, MediPharm’s introduction of thermoformed PS film packaging could mark a significant shift in how pharmaceutical products are packaged and delivered to the market.
Revolutionizing Folded Box and Pharmaceutical Thermoforming Packaging—PVC Sheets Date: August 13, 2023 Location: Shanghai, China Key Players: Leading packing manufacturers, pharmaceutical companies, environmental advocates Event Summary: In what could emerge as the most radical paradigm shift in packaging, Shanghai's top manufacturers yesterday announced increased application of polyvinyl chloride sheets for folded box and pharmaceutical thermoforming packaging. This will change the world in terms of product protection, cost efficiency, and manufacturing versatility. Background: Durability, flexibility, and cost represent some of the most preferred characteristics of PVC, and it has thereby found a place in most industries. However, recent developments in manufacturing PVC sheets raise renewed interest in using the material for special applications in pharmaceutical packaging and other consumer products. Cause and Course of Events: The trend of using PVC sheets in folded box and pharmaceutical packaging started this year when a number of packaging specialists, associated with different pharmaceutical companies, launched an all-inclusive study regarding the effectiveness of the material. Their conclusions, published in June 2024, pointed to some main advantages of PVC sheets, first of all related to their better defense against moisture, oxygen, and light—parameters that play a very important role in the preservation of pharmaceutical products. After the research, some leading packaging companies in Shanghai started to apply PVC sheets in their production lines within a very short period of time. It is the possibility of easily cutting, folding, and thermoforming the material into desired shapes that allows these companies to fulfill the tough requirements from pharmaceutical industries while offering beautiful and functional packaging to consumer products. Result: Beginning with the adoption of PVC sheets, fruitful results have already started to show. Pharmaceutical firms are reportedly found to declare that most of the problems related to packaging, such as contamination and damage of the product during transportation, have reduced considerably. Consumers have also welcomed the enhanced protection and longer shelf life of products packaged with PVC. Moreover, this reduces the overall production cost of PVC sheets, thereby enabling the manufacturer to maintain a competitive price and upgrade the quality of packaging. Impact and Future Prospects: Interest in PVC sheets for folded box and pharmaceutical thermoforming packaging has been quite successful, and other markets, like food and electronics, where solid, protective, and cost-efficient packaging is a must, may get attracted to it. Environmentalists still are wary and remind that without recycling programs, harm to the environment from PVC will only continue to grow. As innovations further the development in the packaging industry, PVC sheets can only play an ever-increasing role as a solution providing a reliable performance-cost-consumer safety balance for manufacturers. With Shanghai at the helm of this change, its packaging sector is well on course to lead global efforts towards improving products' packaging through strategic material use, such as PVC.
Durability: ABS sheets are highly resistant to impact and very tough, hence ensuring that the conductive panels undertake physical stress and other related harsh environments.
Polyvinyl chloride (PVC) is one of the most widely used plastics in the world, and its application in the medical packaging industry has become indispensable due to its versatility, durability, and cost-effectiveness. Here, we explore the various applications and benefits of PVC in the medical packaging field.