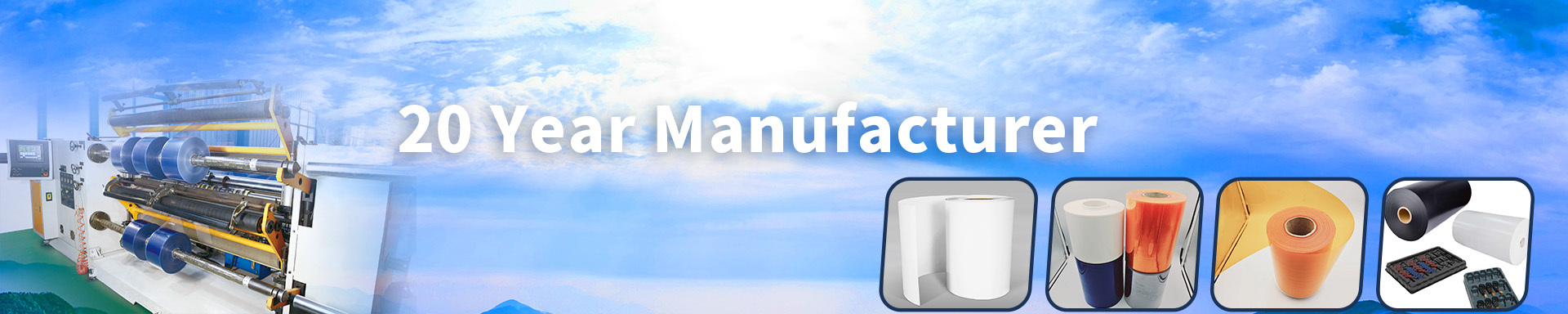
rigid pvc film primary packaging orange color
Selection and improvement of orange rigid PVC film pharmaceutical packaging materials
Selection of high-quality PVC resin: Select PVC resin with high purity and few impurities as the base material to ensure that the film has good physical properties and chemical stability, and reduce potential impact on pharmaceuticals
- top leader plastic
- China
- 10-15 working days
- 1900 tons/month
- Information
pvc film primary packaging orange color
Add appropriate additives: Improve the performance of orange rigid PVC film by adding specific additives. For example, adding heat stabilizers can improve the heat resistance of the film and prevent degradation due to heat during processing and storage; adding plasticizers can adjust the flexibility of the film to a certain extent, making it easier to form and use, but be careful to choose plasticizers that meet pharmaceutical packaging standards to avoid adverse effects on drugs; add colorants to obtain the desired orange color, ensure the safety and stability of the colorants, and do not migrate or seep into the drugs.
Adopting modification technology: such as maleic anhydride functionalized modified PVC resin, which can significantly enhance the energy required for the destruction of PVC resin macromolecular chains, inhibit the excitation of chlorine atoms on macromolecular chains, and improve heat resistance. At the same time, adding nano-bentonite particles modified by coupling agents, connecting with macromolecular chains to form a stable three-dimensional network structure, effectively eliminating the self-catalytic degradation of hydrogen chloride on PVC, and improving long-term thermal stability.
Production process control
Purify the production environment: The workshop producing orange rigid PVC film should maintain a high standard of cleanliness, usually with a purification level of 100,000, to create a clean area environment with constant temperature, constant humidity, and strict pressure difference to prevent dust, microorganisms and other impurities from contaminating the film and ensure product quality.
Precise extrusion and calendering: Use high-precision planetary extruders and multi-roll calenders to accurately control parameters such as temperature, pressure and speed of extrusion and calendering to ensure uniform film thickness, smooth surface, good physical properties and appearance quality. For example, by adjusting the gap and speed ratio between the rollers of the calender, the thickness and surface flatness of the film can be controlled.
Online monitoring and testing: Install online monitoring systems on the production line, such as thickness detectors, optical detectors, etc., to monitor the film's thickness, transparency, color uniformity and other indicators in real time, and promptly detect and correct deviations in the production process. At the same time, equipped with professional quality testing instruments, such as oxygen permeability detectors, water vapor permeability detectors, burst strength meters, tear strength meters, etc., to test the finished products in accordance with all quality inspection items stipulated by the state to ensure that the film meets the relevant standards for pharmaceutical packaging.
Packaging design and structural optimization
Blister packaging design: According to the shape, size and quantity of the medicine, design a suitable blister shape and specification so that the medicine can be tightly fixed in the blister to prevent movement and collision during transportation and storage. The depth and spacing of the blister should be reasonable, both to ensure the storage space for the medicine and to facilitate consumer access. At the same time, the heat sealing process is used to seal the orange hard PVC film with the medicinal aluminum foil to form a good barrier effect to prevent the medicine from moisture, oxidation and contamination.
Multi-dose packaging design: For some drugs that need to be used according to the course of treatment or dosage, multi-dose packaging can be designed, combining multiple blisters or medicine bags in one package, and equipped with clear instructions for use and dosage indications to facilitate patients to use and manage drugs. For example, a compartmentalized or layered design is used to package different doses or different types of drugs separately to avoid confusion.
Easy-to-open structure design: Considering the convenience of patient use, easy-to-open structures such as tearing holes, pull rings or easy-to-peel films are added to the packaging design. These structures should ensure that the packaging is sealed, so that patients can easily open the package and take out the drugs, while avoiding contamination or damage to the drugs during the opening process.
Quality control and management
Establish strict quality standards: According to relevant national laws and regulations and pharmaceutical industry standards, formulate internal quality standards for orange rigid PVC film pharmaceutical packaging, clarify the specific requirements of various indicators, including appearance, size, physical properties, chemical properties, microbial limits, etc., to ensure the consistency and stability of product quality.
Supplier management: Strictly evaluate and screen suppliers of raw materials such as PVC resin, additives, colorants, etc., select suppliers with good reputation and quality assurance capabilities, and establish long-term and stable cooperative relationships. Regularly inspect and review the raw materials provided by suppliers to ensure that the quality of the raw materials meets the requirements.
Batch management and traceability: Detailed production records and identification of each batch of orange rigid PVC film, including information such as raw material batch, production time, production equipment, and production personnel, to achieve product traceability. Once a quality problem is found, it can be quickly traced back to the relevant batch of products, and appropriate measures can be taken to deal with it, such as recall, scrapping, etc., to ensure the safety and quality of the drug.\
Within 15-20 days after received payment...more