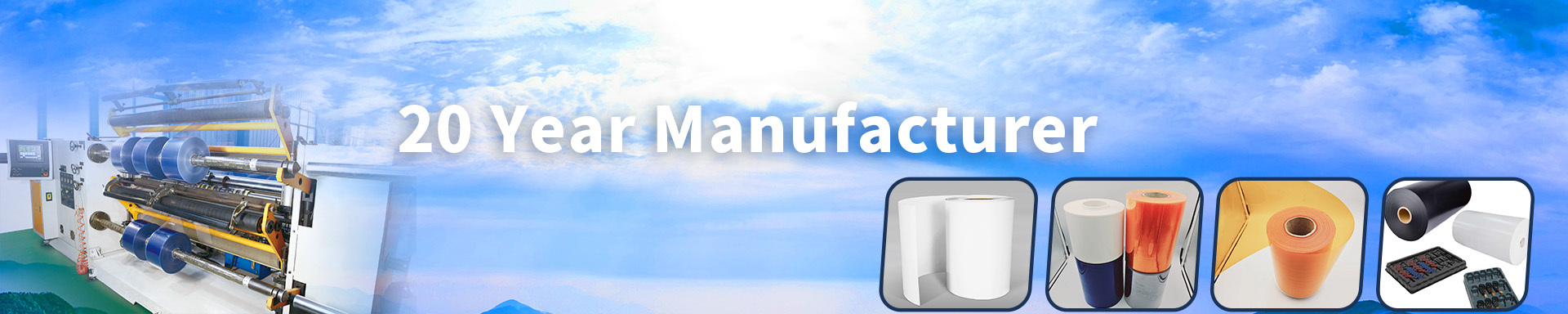
150 Micron Cold Forming Alu Alu Bottom Foil for Pills Packing
2024-12-31 15:04150micron cold forming Alu Alu Bottom Foil for Pills Packing As in every dynamic era concerning the packaging of pharmaceutical products, the material preferred brings along the most integral characteristics and assures medication integrity, potency, and safety. Out of various types, the cold form foil is now considered the paradigm to transform the packaging method applied and gives a new perspective towards it.
I. Debunking the Mystery of the Material
Behind this magnificent packaging solution, the shining hero is, no doubt, the metal-aluminum-and all its phenomenal qualities combined. In purest form, it is lightweight with amazing strength. Blanked out in a foil form in thicknesses up to 150 microns, there's a great deal of dexterity applied. This foil must just be thick enough to perform in a most commendable defense from the bruises associated with handling, transport, and storage. Imagine a consignment of fragile pills taking a rough ride on bad roads or jostling around in crowded warehouses, this foil serves as an eternal protector of pills against any damage that would render them ineffective.
Cold forming is a wonder to behold as far as manufacturing goes. Unlike the more traditional methods of forming, which rely on high heat to mold materials, cold forming takes advantage of the natural malleability of aluminum at room temperature, though it does so with the exertion of considerable mechanical force. This is very important in the pharmaceutical world, where many active ingredients in medications are sensitive to heat. The slightest rise in temperature when packaging said pills could start chemical reactions that degrade the potency of the pills.
With cold forming, the pharmaceutical companies are able to ensure that their products remain in pristine condition, away from the detrimental effects excessive heat can cause. Now, the Alu-Alu construction with its two-layered aluminum takes this ability to protect to new heights that were hitherto unattainable; it is sort of like a double fortress against those outside elements threatening pill quality. This barrier provides an effective seal against moisture, that insidious adversary which can cause pills to dissolve, lose their efficacy, or even foster the growth of noxious mold. Even oxygen, so necessary for life, with its propensities to initiate processes of oxidation that can wreak havoc on active ingredients, finds itself locked out. And let's not forget light, especially ultraviolet rays, which can initiate photochemical reactions degrading certain drugs. The opacity of the aluminum foil acts like a sure sentinel, protecting the pills from light-induced degradation.
II. Multifaceted Advantages in Pill Packing
Fortress-like Protection
The 150 micron cold forming Alu Alu bottom foil is made up of two layers of aluminum. An impervious barrier is thus formed. Imagine a batch of pills being stored in a humid environment, say a tropical warehouse. Without proper protection, the pills would immediately absorb moisture and host a range of problems. With this foil, moisture is repelled, and the pills maintain their chemical integrity. Similarly, this foil provides protection against oxidative damage and photodegradation in highly oxygen-rich regions or upon exposure to sunlight. This is not a luxury but an absolute necessity to ensure that patients take drugs with the same potency as on the day they were manufactured.
A Seal of Security: Tamper Evidence Feature
At a time when counterfeiting and tampering with pharmaceutical products are very current risks, the tamper-evident feature of the Alu-Alu bottom foil is a real game-changer. When pills are sealed in precisely cold-formed foil cavities, any attempt to breach the seal without proper authorization leaves telltale signs: it may be a slight distortion of the foil, a break in the seal line, or visible marks where an unauthorized tool was used. This provides an invaluable layer of security both for the end-users, who can be sure that the medication they are consuming has not been adulterated, and for the pharmaceutical manufacturers themselves, who want to protect their hard-earned reputation. Imagine a patient dependent on some lifesaving drug; he will have peace of mind in knowing that the pill he is going to take has been protected from tampering right from the factory to his hands.
Tailored to Perfection: Customizable Design
Despite its deceptively fragile 150 micron thickness, this foil is a real trouper. It can be carefully cold formed to cradle pills of every imaginable shape and size. Be it the round, popularly consumed tablets, sleek oval-shaped capsules, or the irregularly shaped ones for more specialist treatments, the foil presses out with precision. This kind of customized fit does not allow pills to be in a state of suspense, chip, or incur damage while in transit. Moreover, it presents professionalism and an element of caring. At the same time, the pharmaceutical companies take the chance to enhance brand identity. During the cold forming process, they can emboss logos, batch numbers, or even educational messages onto the surface of the foil. That turns the packaging from being just a protective shell into a marketing and informational tool, being able to connect with patients at a much deeper level.
Extending the Lifespan: Shelf Life Extension
Due to its exceptional barrier properties, 150-micron cold-forming Alu-Alu bottom foil is an elixir for increasing the shelf life of pills. Drugs sensitive to environmental conditions, such as certain antibiotics or vitamins, can maintain potency and quality for a longer time. This has wide implications. It reduces the expired drugs waste, which, apart from being an economic drain on pharmaceutical companies, is also a waste of precious resources. This further ascertains that even the patients from remote areas, or those with limited access to pharmacies, can confidently be assured that the medicines they buy will remain effective for a long time. It also smooths out the logistical troubles of pharmaceutical supply chains through the accommodation of flexible storage and distribution schedules.
III. Dances of Production and Quality Control
Manufacturing 150-micron cold-forming Alu-Alu bottom foil is actually conducting a symphony with some of the most advanced manufacturing processes. Everything starts right from the procurement of high-purity aluminum, much of which is mined and refined with the utmost care. This raw material then goes through a series of state-of-the-art machinery and processes to reach the desired thickness and surface finish.
The unsung heroes during cold forming are precision molds made to micron-level accuracy. These are designed to apply just the right amount of pressure in shaping the foil to its final form while still maintaining the integrity of the aluminum layers. But that is not all, for the quality control measures are so interwoven in every step of the way.
This involves the testing of barrier properties of the foil. It has specialized equipment that can detect the minutest amount of moisture, oxygen, or light transmission. The integrity of cold-formed seals is literally put under a microscope. Any hint of a potential leak or weakness is flagged and rectified immediately. Trained technicians conduct visual inspections with an educated eye to ensure that the foil surface has no defects in the form of scratches, dents, or uneven thickness.
Samples are typically taken from the production line for tests to determine their compatibility with different types of pills to ensure that there is not some sort of unforeseen chemical interaction that could undermine the quality of the drug in question. It's painful, but one that has to be done to ensure the safety and effectiveness of the final packaged product.
IV. Navigating the Environmental Landscape
While aluminum is intrinsically recyclable, the manufacture and discarding of pharmaceutical packaging require a more sophisticated approach. Fortunately, the Alu-Alu bottom foil, at the end of its useful life, can be recycled into other products. Facilities around the world that recycle these materials have developed complicated processes to recover the aluminum through melting and reforming it into new products. This reduces the demand for virgin materials and thus preserves valuable natural resources while decreasing energy consumption and the associated greenhouse gas emissions linked to aluminum production.
Pharmaceutical companies, now increasingly environmentally conscious, have begun taking matters into their own hands. The companies have been working with their packaging suppliers to make their designs more environmentally friendly, such as through waste reduction and maximizing recyclability. Some are even exploring ways of encouraging consumers to recycle used pharmaceutical packaging, through incentives or educational campaigns, for example.
V. Real-World Applications and Success Stories
In the busy corridors of pharmaceutical manufacturing plants around the world, the 150 micron cold forming Alu Alu bottom foil is making a tangible difference. Take for example one of the leading manufacturers of life-saving heart medications. They were having problems with the shelf life of their pills, particularly in regions that are very humid. They had observed, with this superior foil packaging, an incredible extension of shelf life for their products. This would mean that fewer drugs would reach their expiration dates and be disposed of, which reduces the waste of medications and allows more access to patients. Another example is a small, boutique pharmaceutical company proud of its artisanal way of formulating drugs. They were in search of packaging that would protect their unique, handcrafted pills and add value to the brand image. They were able to emboss their elegant logo and give detailed instructions on the customized Alu Alu bottom foil. Further, it prevents damage in transit while adding to a great customer unboxing experience, enhancing brand loyalty in the process.
VI. Future Horizons: Innovations and Trends
The future of 150-micron cold forming Alu-Alu bottom foil in pill packing is brilliant, with technology forging ahead and the expectations of consumers still shifting. A number of researchers are studying the embedment of smart technologies within the foil. For example, envision a foil capable of detecting changes in temperature, humidity, or even chemical composition changes of the pills inside it. Such a foil would be able to provide warnings if the conditions are approaching levels that may affect the quality of the drug.
In the field of sustainability, efforts are being made to further optimize the process of recycling. New methods in the separation of the aluminum layers are being developed so that less energy is used to recycle it. Furthermore, there is a growing trend towards using recycled aluminum in the production of the foil itself, closing the loop and creating a more circular economy.
The design aspect is also set to change. With the rise of personalized medicine, packaging will have to be even more adaptable. The 150 micron cold forming Alu Alu bottom foil may soon be tailored not only for the shape and size of the pill but also to accommodate the particular needs of a patient, maybe with removable sections for partial dosing or child-proofing features that are seamlessly integrated into the design.
Conclusion The 150 micron cold forming Alu Alu bottom foil has been indispensable in packing pills. Blending robust protection, customized design, tamper evidence, and environmental friendliness, this product has become a darling for the pharmaceutical industry. As we look to the future, with continued innovation and a focus on sustainability, this remarkable material will continue to play a crucial role in ensuring the safe and effective delivery of medications to patients across the globe.