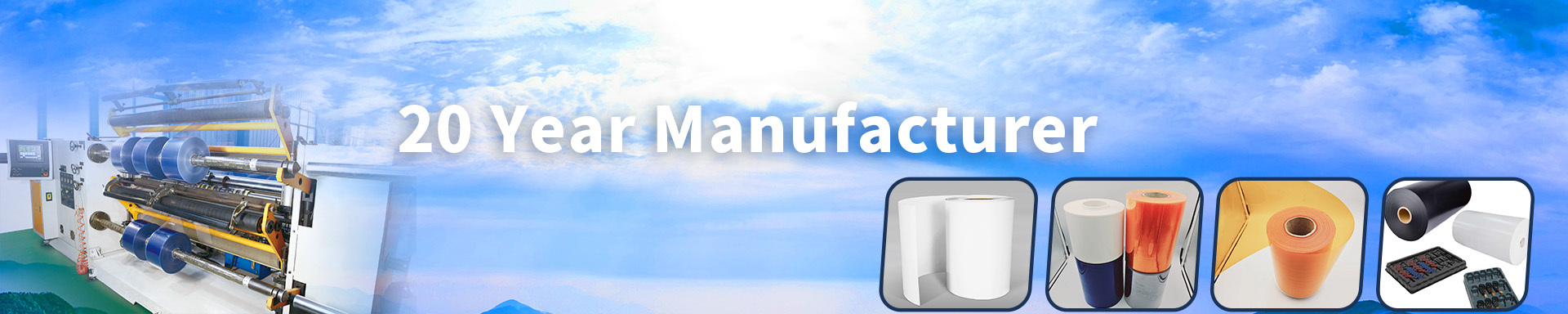
PVC FILM Characteristics and Applications of Colored PVC Protective Films for Steel Plates
2025-05-21 17:14Characteristics of Colored PVC Protective Films
Material Composition and Structure
Colored PVC protective films are made from polyvinyl chloride, a synthetic plastic polymer known for its durability, flexibility, and cost-effectiveness. These films are typically coated with a pressure-sensitive adhesive (PSA), such as rubber or acrylic, which ensures secure adhesion to steel surfaces while allowing for clean, residue-free removal. The colored aspect of these films, achieved through pigmentation or co-extrusion processes, adds both functional and visual benefits. For instance, colors like blue, black, white, or transparent variations help distinguish protected surfaces, indicate processing directions, or enhance visibility during handling. The films are available in thicknesses ranging from 50 to 120 microns, with adhesive strengths tailored to specific surface types and processing requirements.
Adhesion and Peelability
One of the standout features of colored PVC protective films is their excellent adhesion strength, which ensures they remain firmly attached to steel plates during rigorous processes like cutting, bending, stamping, or deep drawing. The adhesive is designed to provide stable bonding without leaving residue upon removal, a critical factor for maintaining the pristine condition of steel surfaces. For example, films with rubber-based adhesives offer fast bonding and high tack, ideal for smooth or mirror-finish steel plates, while acrylic adhesives provide better long-term stability and transparency for aesthetic applications.
Elasticity and Conformability
PVC films are highly elastic and conformable, allowing them to adapt to the contours of steel plates, including complex shapes or curved surfaces. This elasticity is particularly valuable in deep-drawing applications, where the film must stretch without tearing or losing adhesion. Blue PVC protective films, for instance, are specifically designed for multi-stage deep drawing, with a nominal thickness of around 70 microns and a rubber adhesive layer that withstands high stress without compromising protection.
Durability and Environmental Resistance
Colored PVC protective films are engineered to withstand harsh manufacturing environments, including exposure to abrasion, friction, and limited UV radiation. While prolonged sunlight exposure (beyond a few hours) can degrade the adhesive and cause residue transfer, certain films are formulated with UV-resistant properties for short-term outdoor use, offering up to 6 months of protection. Additionally, these films resist corrosion, dust, and contamination, ensuring that steel plates remain free from scratches and scuffs throughout their journey from production to end use.
Aesthetic and Functional Color Variations
The use of color in PVC protective films serves multiple purposes. Transparent films allow for visual inspection of the steel surface without removal, while opaque colors like black-and-white or blue enhance visibility and provide UV protection. For example, a black-and-white co-extruded PVC film combines UV absorption (black layer) with UV reflection (white layer), offering superior protection for steel plates stored outdoors. Colored films also aid in identifying polishing directions or surface finishes, as printed arrows or stripes can indicate the grain of brushed or polished stainless steel.
Applications of Colored PVC Protective Films for Scratch Prevention
Protection During Manufacturing Processes
Steel plates, particularly stainless steel and aluminum, undergo demanding processes such as laser cutting, bending, drilling, and stamping, all of which pose risks of surface damage. Colored PVC protective films act as a robust barrier, absorbing impacts and preventing scratches during these operations. For instance, Novacel’s PVC-free films, though not the focus here, highlight the importance of conformable films for deep drawing, a process where PVC films excel due to their elasticity. A blue PVC protective film with a rubber adhesive is particularly suited for multi-stage deep drawing, ensuring the steel surface remains intact even under high mechanical stress.
Safeguarding During Transportation and Storage
Transportation and storage expose steel plates to risks like abrasion, dust, and handling marks. Colored PVC protective films provide a protective shield, ensuring that surfaces remain flawless. For example, during shipping, a glossy stainless steel plate covered with a translucent blue PVC film can arrive at its destination without scratches, enhancing customer satisfaction and reducing costly returns. The film’s easy-peel feature allows workers to remove it quickly without leaving adhesive residue, revealing a pristine surface ready for installation or further processing.
Specialized Applications in Deep Drawing
Deep drawing is a critical process in shaping steel plates into products like kitchen appliances or automotive components. Colored PVC protective films, particularly blue variants, are designed to withstand the intense stretching and pressure of this process. Their flexibility ensures they adhere securely without tearing, protecting the steel from drawing marks or scratches. However, care must be taken during laser cutting or plasma cutting, as PVC films can release toxic hydrochloric acid fumes when burned. To mitigate this, cutting should be done from the unprotected side or with oxygen assistance.
Enhancing Aesthetic Appeal in Consumer Products
In industries like appliances and automotive manufacturing, colored PVC protective films play a dual role: they protect surfaces and maintain aesthetic appeal. For example, a stainless steel refrigerator door covered with a black-and-white PVC film arrives at the showroom in pristine condition, free from scratches or scuffs. The opaque color hides minor imperfections during transit, ensuring the product looks flawless when the film is peeled off by the consumer. This not only enhances the product’s marketability but also reduces the need for costly repairs or replacements.
Customized Solutions for Specific Surfaces
Different steel finishes—such as mirror, brushed, or high-gloss bright annealed (BA)—require tailored protective films. Colored PVC films can be customized with varying adhesive strengths and thicknesses to match the surface texture. For instance, a low-viscosity adhesive is ideal for smooth, glossy steel plates, while a stronger adhesive is better suited for textured or matte finishes. This customization ensures optimal adhesion and protection without compromising the ease of removal.
Practical Considerations for Using Colored PVC Protective Films
Surface Preparation
To maximize the effectiveness of PVC protective films, proper surface preparation is essential. Steel plates must be clean, dry, and free from dust, oils, or contaminants. Poor surface preparation can lead to adhesion issues, such as premature peeling or residue transfer. A simple cleaning with isopropyl alcohol or a similar solvent can ensure a strong bond between the film and the steel surface.
Application Techniques
Applying colored PVC protective films requires care to avoid wrinkles or air bubbles, which can compromise protection and aesthetics. The film should be applied slowly and evenly, starting from one edge and using a squeegee to smooth out air pockets. For large steel plates, automated application systems can ensure uniform adhesion, reducing the risk of imperfections.
Environmental Considerations
While PVC protective films are highly effective, they are less environmentally friendly than alternatives like polyethylene (PE) films, as PVC is difficult to recycle. However, their durability and cost-effectiveness make them a preferred choice for many applications. Manufacturers should weigh the environmental impact against the functional benefits and consider proper disposal methods to minimize ecological harm.
Removal and Residue Management
The clean removal of PVC protective films is a key advantage, but prolonged exposure to sunlight or extreme temperatures can degrade the adhesive, leading to residue transfer. To avoid this, films should be removed within the recommended time frame (typically within a few months) and stored away from direct sunlight. If residue occurs, it can often be removed with a mild solvent, though this adds an extra step to the process.
Case Studies and Real-World Examples
Stainless Steel Appliance Manufacturing
A leading appliance manufacturer uses blue PVC protective film to safeguard stainless steel refrigerator panels during production and shipping. The film’s translucent nature allows quality control teams to inspect the surface without removal, while its rubber adhesive ensures secure bonding during stamping and assembly. Upon delivery, the film is easily peeled off, revealing a scratch-free, mirror-finish surface that meets consumer expectations.
Architectural Steel Panels
In a large-scale architectural project, colored PVC protective films were applied to brushed stainless steel panels used in a building facade. The black-and-white film provided UV protection during outdoor storage and transportation, preventing scratches and corrosion. The printed arrows on the film helped workers align the panels correctly, ensuring a seamless installation process.