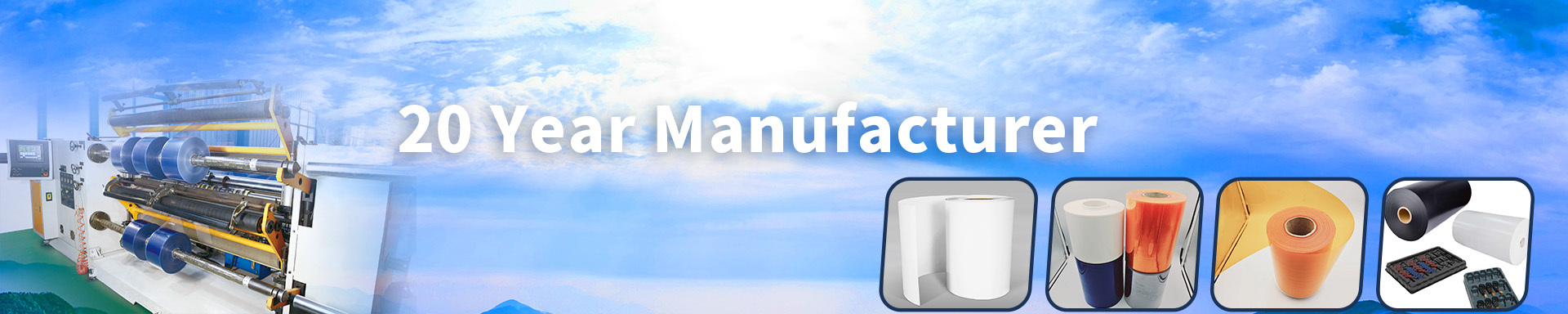
News
material: disposable PLA cornstarch size:240*190*50mm usage : food tray, takeout plate,
ITEM:TL-PVC-0047 Thickness:0.008-2MM Width:100-1350MM color:white blue red orange black customization Roll core:3-7” feature:Water proof Usage:Color sheet, deco film,cover film capability:5000TON/MONTH Sample:Free less than 10KG
Transparent Biaxially Oriented Polypropylene (BOPP) film has become an essential material in various industries due to its unique properties and versatility. This article will explore the extensive applications of transparent BOPP film in different fields, including food packaging, stationery, tobacco, and gift packaging. We will discuss its advantages, manufacturing process, and future prospects.
In the world of materials and printing, PVC printable film stands out as a versatile and remarkable product with a wide range of applications. From advertising and signage to personal projects and creative endeavors, this material has proven to be an invaluable asset.
In today's world of design and decoration, colored PVC film has emerged as a highly versatile and innovative material that is transforming the way we think about aesthetics and functionality. From creating stunning colored walls in interior design to enhancing the beauty of lampshades and serving as an essential tool for color selection in the form of color cards, colored PVC film is making its mark in various fields.
Tableware, whether it's delicate porcelain, fine glassware, or sturdy cutlery, requires protection to maintain its pristine condition. Transparent PET film offers an excellent solution for safeguarding tableware during storage and transportation. The crystal-clear transparency of the film allows the beauty of the tableware to shine through while providing a protective barrier. It prevents scratches, dust, and moisture from damaging the tableware. When wrapped around tableware items, the film conforms to their shape, providing a snug fit and ensuring that they remain secure.
In conclusion, biodegradable PLA film is a revolutionary material that is transforming the way we package and consume food. Its applications in different fields are diverse and growing, offering a sustainable alternative to traditional plastic materials. As we move forward, let's continue to embrace and promote the use of PLA film and other eco-friendly materials to create a more sustainable future for ourselves and the planet.
In an era where environmental consciousness is on the rise, biodegradable materials have emerged as a crucial solution to combat the growing problem of plastic waste. One such remarkable material is Polylactic Acid (PLA), a biodegradable polymer that has found extensive applications in various fields. In this article, we will explore the vivid and diverse uses of biodegradable PLA film, particularly in the areas of tableware trays, food trays, and fruit trays.
Transparent Pet film, with its unique properties and versatility, has found extensive applications in various industries. In this article, we will explore the uses of transparent Pet film in different fields at room temperature, including blister jewelry packaging, blister tool packaging, blister pharmaceutical packaging, and insulation boards. Through vivid descriptions and real-life examples, we will showcase the importance and advantages of this remarkable material.
Blister Pharmaceutical Packaging The pharmaceutical industry also relies heavily on transparent PET film for packaging. Similar to food packaging, the transparency of PET film allows for easy inspection of the contents, ensuring the integrity and quality of the medications. PET film provides a barrier against moisture, light, and oxygen, which can degrade the potency of drugs. This is especially important for sensitive medications such as tablets, capsules, and powders.